Challenges can be a powerful catalyst for unity, as shown by a student team breaking new ground in the development of ballistics armor through innovative 3D printing technology.
This summer, three undergraduates and one graduate mechanical engineering student are immersing themselves in the Composites Lab. They are collaborating with mechanical engineering Professor Eltahry Elghandour through the Summer Undergraduate Research Program (SURP), which provides students with invaluable hands-on research experience alongside faculty members.
“Struggles have united us, but the small successes have kept us motivated,” said Jedidiah Jimenez, who was in the lab with fellow seniors Roha Ali, Jack Bride and graduate student Lukas Kolbl during a recent work session.
Their mission: to create adaptable, bullet-resistant armor by integrating Kevlar fiber, carbon-reinforced filament and impact-insulating silica into a multi-material solution. The project targets lower-end armor designed for scenarios that don’t require withstanding high force, such as law enforcement training or use by private security personnel.
Despite significant progress, the team has faced major roadblocks, the most critical being a testing machine that has been out of order for nearly a decade. Undeterred, they continue to push forward.
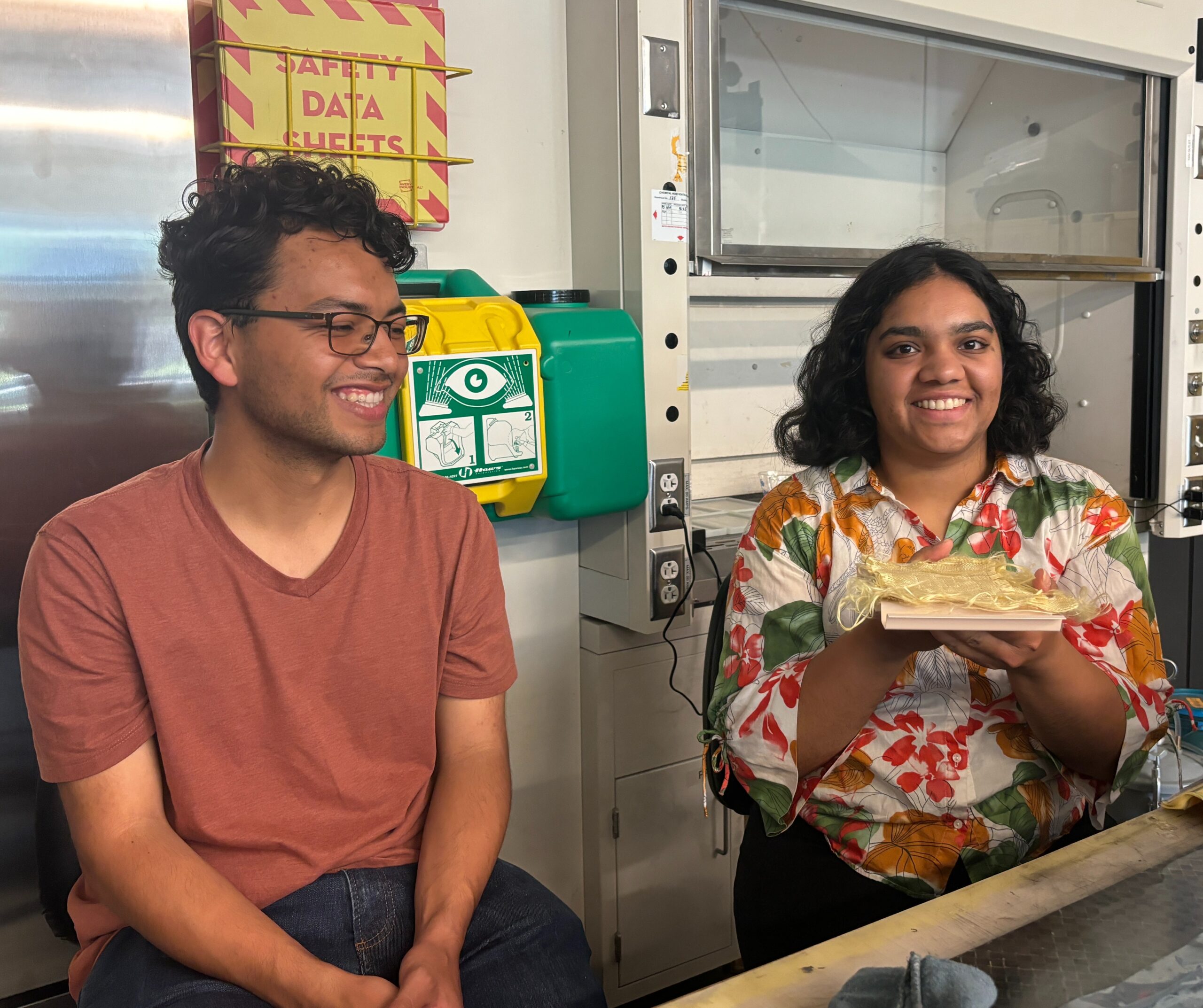
Chaos and Creativity
Bride describes the Composites Lab as a lively and dynamic environment with just enough chaos to keep things interesting.
Amid the materials and molds, he pulls out an extremely detailed diagram he created for the drop-weight impact testing machine. Recruited for his diagnostic expertise and 3D printing skills, Bride is tackling the challenge of repairing this out-of-warranty device, which has stumped students and faculty for years. Without the machine, the team can’t simulate the impact of a 9 mm bullet in the lab.
“We have employed everyone in our mission to fix it,” said Ali, as the team discussed the intense Learn by Doing approach the machine has demanded.
As they close in on a solution, the team is making strides in printing Kevlar — a strong, heat-resistant synthetic fiber — that can be integrated into a vest. Traditional vests are often made of metal, limiting their performance and flexibility, explained Jimenez.
Their innovative process aims to reduce costs and create vests that can bend and flex, tailored to the user’s dimensions. This adaptability offers significant advantages over traditional rigid armor.
Another challenge they face is ensuring consistent material quality and avoiding defects in the 3D-printed parts, Jimenez noted. This involves refining the 3D printing process for better performance and studying how design factors like fiber volume, reinforcement strategy and infill pattern affect the armor’s strength and durability.
Jimenez has also brought his proficiency in a software program that allows the team to experiment with the structure of the material inside the Kevlar pocket. Team members huddle around his laptop screen as he demonstrates how he can manipulate the shape and orientation of complex structures, such as gyroid and auxetic patterns.
“The possibilities really are endless,” he said as the team emphasized the importance of setting limits on their designs.
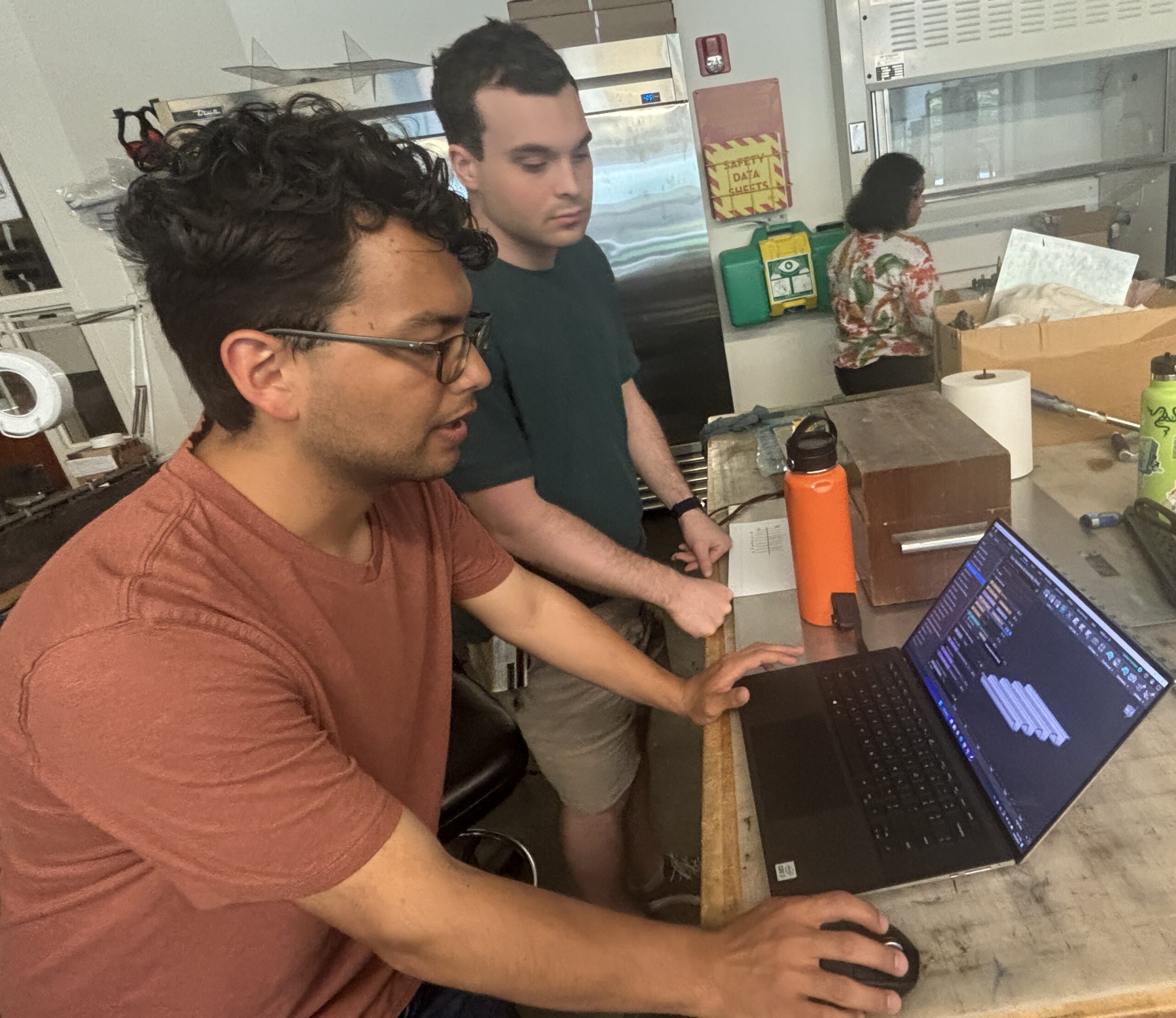
Creating a Weird Sandwich
Kolbl has been a key contributor, leveraging his knowledge from his graduate studies in corrugated geometry – a design involving repetitive folds or ridges that can enhance material performance.
“Corrugated structures are super shock-resistant,” he said. “Our goal is to further characterize these impacts and explore how corrugated geometry can enhance durability.”
Manufacturing these complex geometries can be achieved at a relatively low cost, according to the team.
Once they determine and 3D print their corrugated structure, it will be coated in silica to add a dampening effect. “We want the silica to absorb the force of impact instead of the body,” said Ali, displaying her silica samples made with different combinations of hardeners and softeners.
Ultimately, the multi-material fibers within the 3D printed parts will be combined with silicon in the pocket.
“In simple terms, we are making a weird sandwich,” Bride said.
Within a month, the team will send their sample to Range Master in San Luis Obispo for ballistics testing. Their indoor gun range will provide a controlled environment for an employee to shoot at a mounted sample with a 9 mm bullet. This range testing will give the team a correction factor and verify their claims.
“The project should be done this summer, but we’ve had some delays,” Ali said with a knowing look, pointing to their nemesis, the impact testing machine. Despite the setback, she and Bride will continue with the project, while Jimenez heads to Sweden for studies in the fall and Kolbl wraps up his thesis. They are proud of the strides they have made and remain hopeful for the project’s success.
As they gathered silica samples and corrugated structures for a group photo, the bond they had forged through their collaborative efforts was clear, reflecting their resilience and dedication.
By Emily Slater
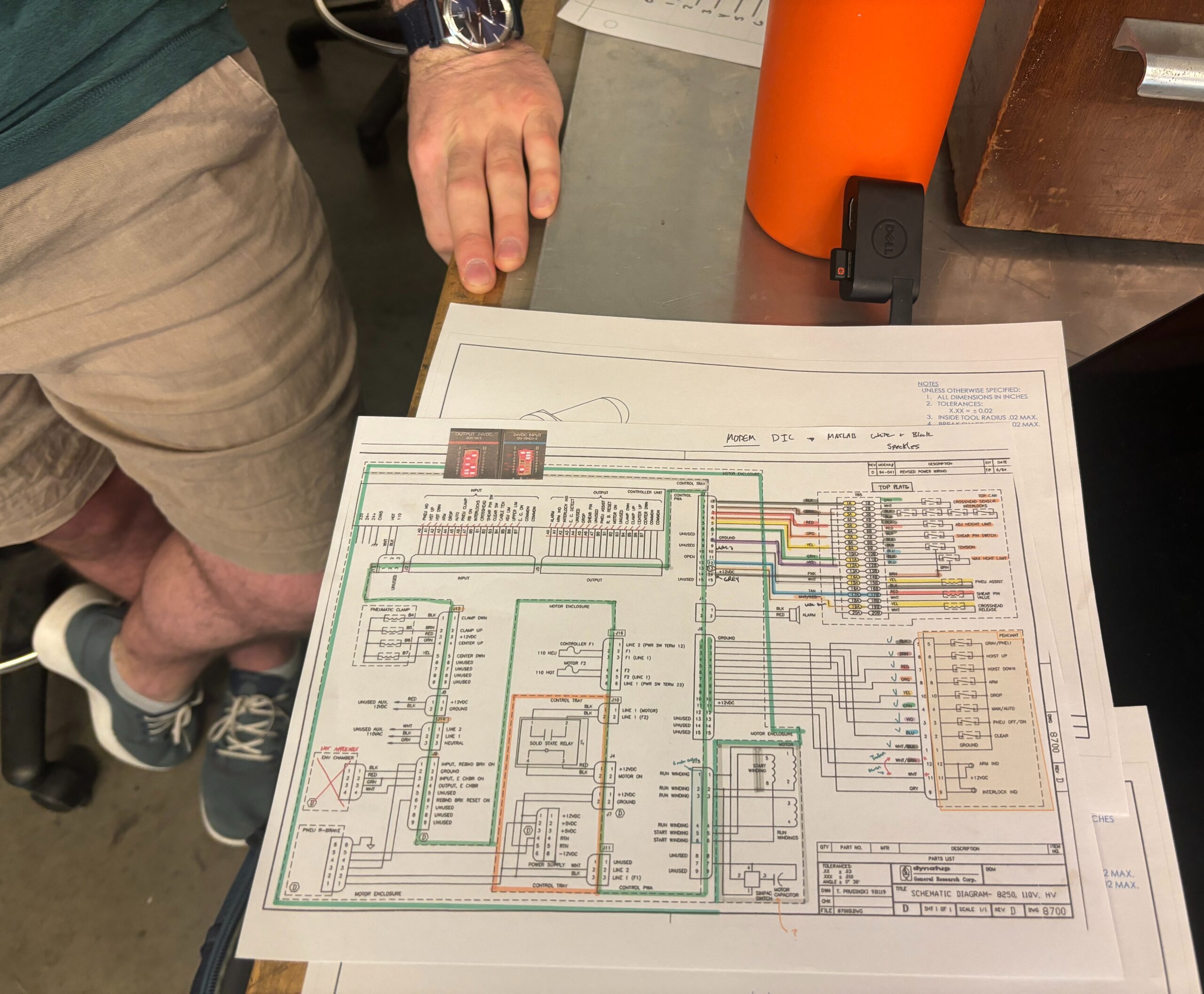