How smart manufacturing is making its way in the industry
Professor Daniel Waldorf wanted to explore manufacturing facilities in hopes of learning more about the future of the industry. After hearing about the progression of smart manufacturing in manufacturing and industrial engineering companies, he sought to learn more about the advancement.
The Industrial and Manufacturing Engineering Department chair took a three-month sabbatical in September 2022 to explore innovative ways the industry is implementing smart manufacturing in Europe, Los Angeles and New York. One of the notable places he visited was the Siemens headquarters in Munich, Germany, where most of the machines are considered to include smart technology.
Smart manufacturing is implemented through sensors that are connected to machinery in factories or elsewhere. The hardware collects the data, which can range from the machine’s temperature to its productivity output. The data is then presented in a single place, like a webpage, for engineers to interpret.
As the industrial and manufacturing engineering industry strives to become more methodical, companies are transitioning toward smart manufacturing to increase efficiency and potentially be more environmentally sustainable.
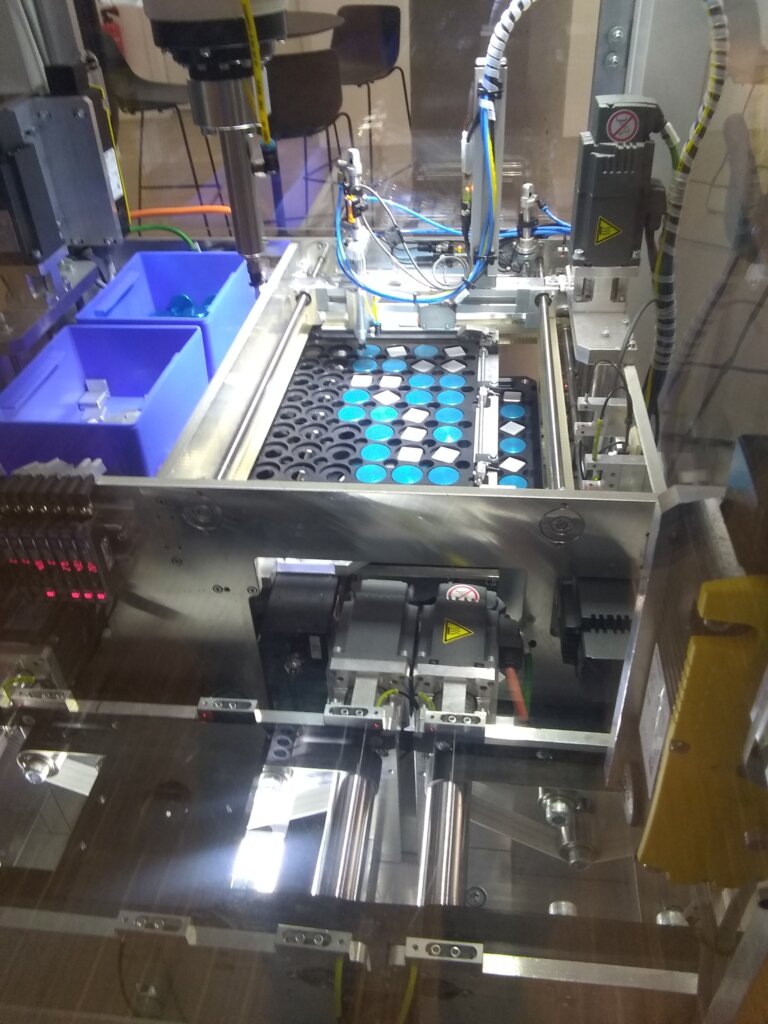
“With smart manufacturing, you can be making better decisions with the information you have,” Waldorf explained.
This process can streamline production by compiling data from several machines at a time and displaying the information in a way that is easy to evaluate. For instance, workers can view how efficiently each individual machine is working without manually checking the technology. It is also a simplistic way to track if a machine breaks down.
“Smart manufacturing answers questions that would be harder to solve in the past,” Waldorf explained. “Now, people can add sensors to devices to read all this information and they can make much better decisions.”
While engineers can manually add sensors that read information from older devices, most newer machines come with built-in sensors, making the process of gathering data easier than ever. Some devices are also guided with lasers that enable the machinery to stay on track.
Because the future of manufacturing and industrial engineering is moving toward smart engineering, Waldorf is considering how to implement what he learned during his sabbatical into his courses.
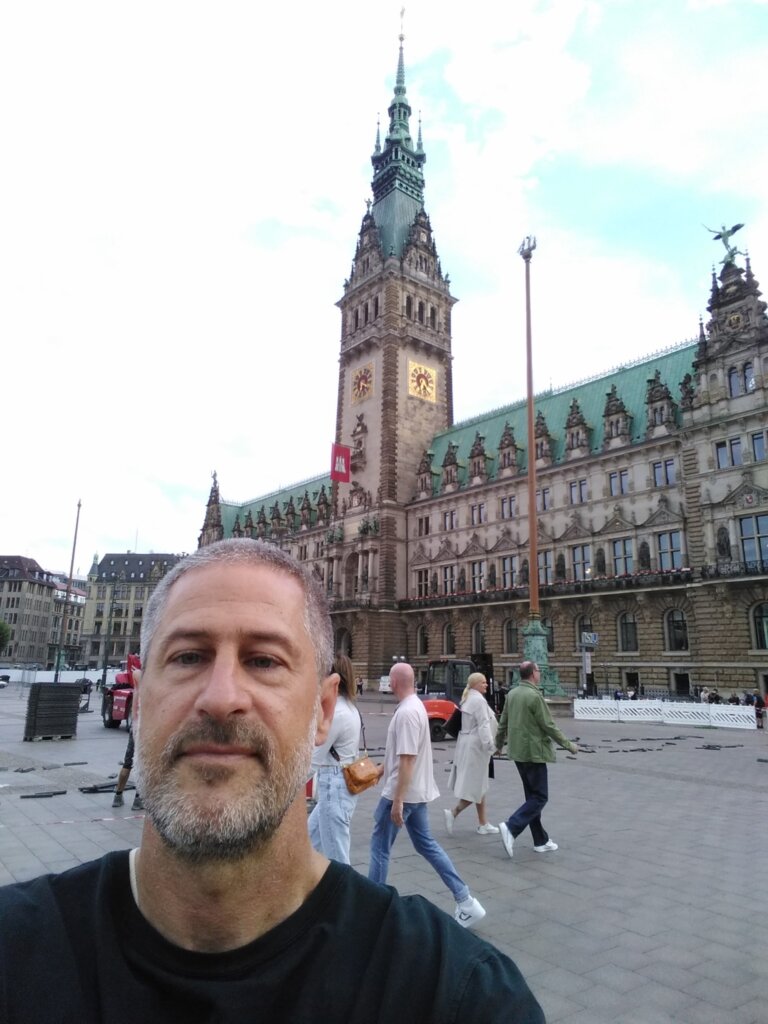
“Smart manufacturing has been something our industry contacts have talked about recently, especially those who are looking to hire our students,” he said. “I wanted my sabbatical and research to bring knowledge and energy that would benefit the whole IME department and that would add real value to students’ education.”
Engineering students across the board have relevant skills related to smart manufacturing. For instance, electrical engineers are needed to properly connect the circuits that monitor the machinery, while computer engineers are needed to interpret the data that comes from the machines.
To further explore smart engineering, Waldorf gathered a team of two students who are working on their own smart manufacturing project. Hendrik Botha (manufacturing engineering) and Tillman Erb (industrial engineering) are setting up an equipment monitoring system using machine sensors. Their goal is to collect real-time data of a machine and transfer it to the internet for data processing and analysis.
“The students have different specialties,” Waldorf shared. “They make a good team.”
Under Waldorf’s guidance, the students should be able to read machine data through a portable development circuit board in the hopes of monitoring its efficiency.
By Taylor Villanueva