Two engineering students who met on a club project to design custom ankle braces for a peer wanted to give a broader group the same chance to make a difference, so they dreamed up a multiyear, interdisciplinary project with the potential to change lives.
Their goal was to go beyond leg braces to construct a wearable robotic device that would require a high level of hands-on learning and ultimately help a student who required assistance walking.
Over four years, more than 75 students have given their energy and expertise to build a robotic exoskeleton – an external frame powered by electric motors – with a final design and functional prototype just around the corner.
“We see light at the end of the tunnel, and it’s exciting,” said Christie Altamura, CEO of Lower-Limb Exoskeleton Assist Project, a multiyear endeavor born out of the EMPOWER Student Association. “We’ve all learned so much along the way.”
LLEAP unveiled its first single-leg prototype of the exoskeleton at the end of the 2022 academic year, with members working toward completion of the final design and prototype in 2024.
Soon, the group hopes to name a student user with a spinal cord injury for their exoskeleton after meeting safety requirements, with past and present members predicting a surreal and satisfying moment when those first steps are taken.
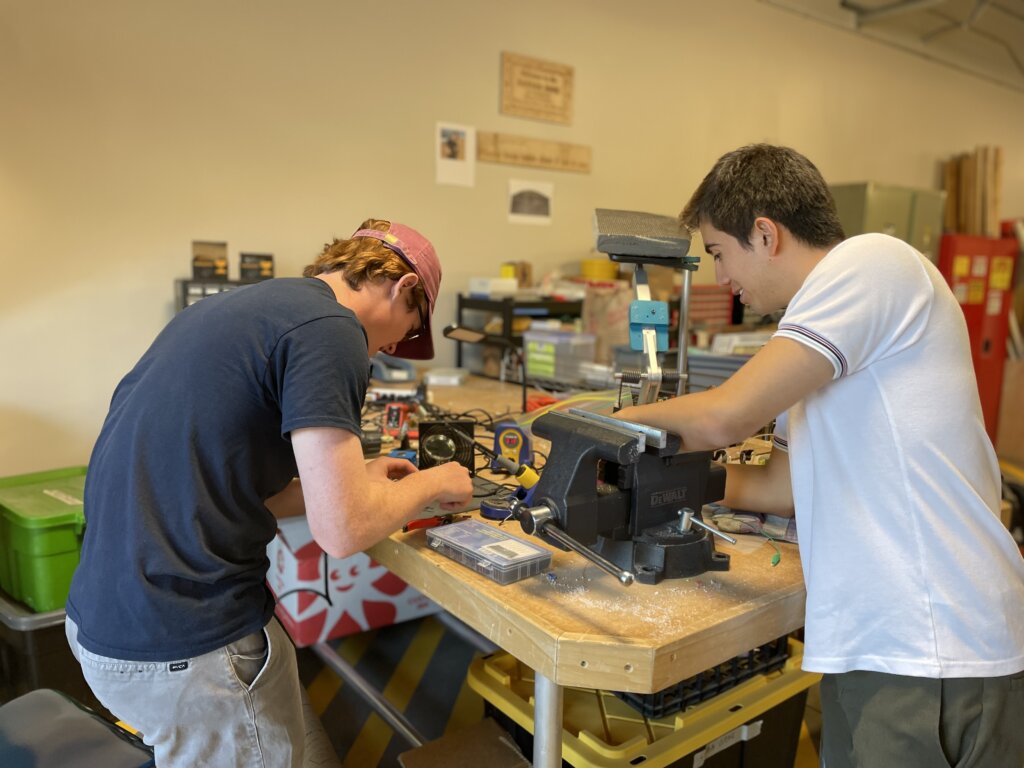
Launching LLEAP
Janis Iourovitski came to Cal Poly as a general engineering major in 2017 and joined engineering clubs – including the club that would eventually be known as EMPOWER – to get a better grasp on the discipline she’d chosen.
The EMPOWER Student Association aims to build technology – prosthetic arms, legs and hands and devices like portable lifts and motorized wagons – that improves someone’s life. Students are assigned to quarterly or yearly design projects as they gain hands-on experience in the TECHE lab.
Iourovitski was named to a yearly project, led by biomedical engineering student Michael Gallagher, to design slimmer, elastic ankle braces for a Cal Poly student with a neurological disorder.
As they designed, experimented and tested, the pair discussed the appeal of a multiyear project that would enable them to pass down knowledge to new members. They also “geeked out,” Iourovitski said, over cybathlon – an international competition intended for people with physical disabilities who use assistive systems.
“Cybathlon opened our eyes to a new community and a cool place to learn about up-and-coming tech,” she explained.
One device – a robotic exoskeleton for someone with no function of the lower body – captivated them with its technical challenges and ability to attract students both inside and outside engineering.
After completing their ankle braces, Iourovitski and Gallagher passed out flyers around campus to gauge interest in an exoskeleton project, drawing over 50 people to an introductory meeting.
They officially launched LLEAP in 2018 and welcomed the first team in 2019.
“It was total chaos,” said Iourovitski, laughing about the beginning stages. “We were asking ourselves questions like, ‘How do we build this? ‘How do we manage this?’ How do we get money to buy sheet metal?’”
Support from faculty, students and industry partners propelled them forward, as interdisciplinary task groups formed, and team leads stepped up.
Iourovitski graduated in 2021, then earned her master’s degree at John Hopkins University and now works with next-generation surgical robots. She continues to root for LLEAP.
“This project fills my heart with so much warmth,” she said. “The students have made it their own, and they’ve taken it much further than I ever could.”
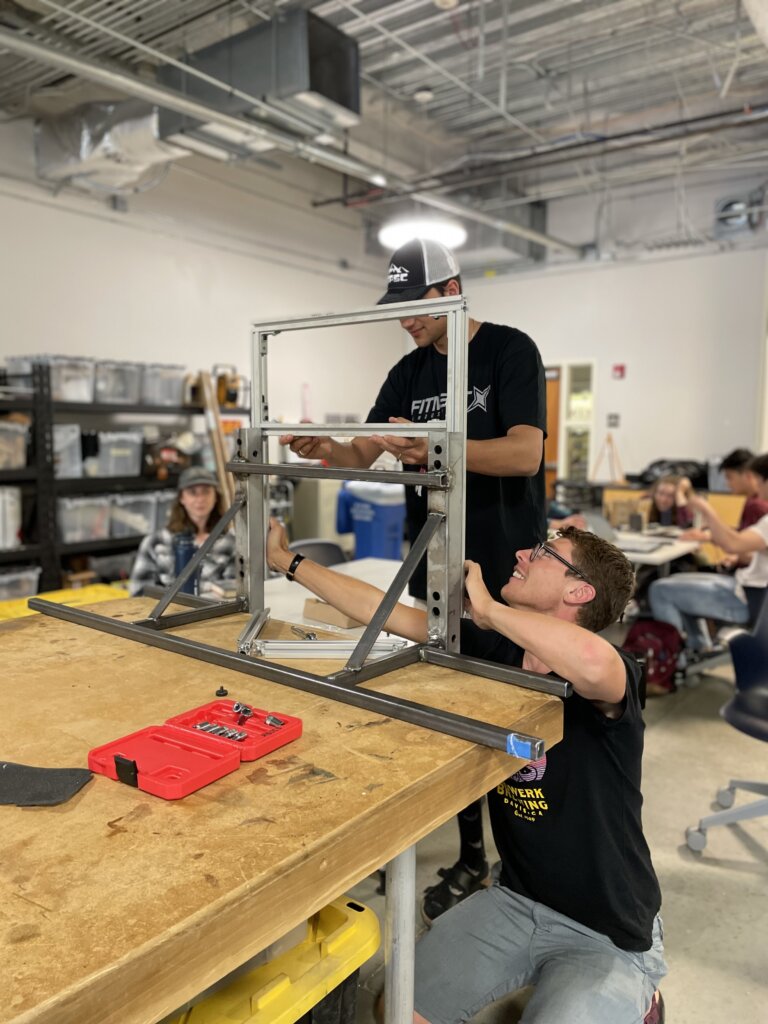
Building a Protype
LLEAP has five interdisciplinary teams this year with members from most of the engineering majors, along with biology and kinesiology.
The prototyping team is in charge of building all the joints, gearboxes and structural components of the exoskeleton, with three subteams focused on the hip, ankle and structures.
The mechatronics team is working to control the motors of the suit, while the sensing and user interface team aims to give the user control of the suit through buttons on the crutches.
Members of the software and engineering team are engaged in ensuring all the components of the suit talk to each other through the middleware Robot Operating System, and a new kinesiology team is ensuring the suit is safe and comfortable.
LLEAP holds general meetings each Thursday, with students invited to join the group any time.
“It’s such a big project, but everyone is passionate and excited about it,” said Altamura, a fourth-year biomedical engineering major. “We’ve all become friends, and there is a true sense of camaraderie.”
LLEAP hit a milestone at the end of the 2022 academic year with the production of their first single-leg prototype. With an adjustable height and weight design, the model has allowed for physical testing.
“The prototype marked the first time that we made something physical,” said Cal Miller, a fourth-year mechanical engineering student and mechanical lead for LLEAP. He joined to apply his skills to a project that could directly help someone.
Their first prototype was large and heavy, Miller said, due to the materials they had and the challenge of scaling a project with computer-aided design. The hip joint alone weighed 25 pounds, according to Altamura.
“Last year was a trial run, and we learned a lot,” Miller said. “Now that we have more experience, we are improving the design and will have a smaller, lighter suit.” Altamura added the hip joint with its new cycloidal design will weigh only 10 pounds.
After they gain robotic control of one leg, the group will manufacture a two-legged, fully functional prototype.
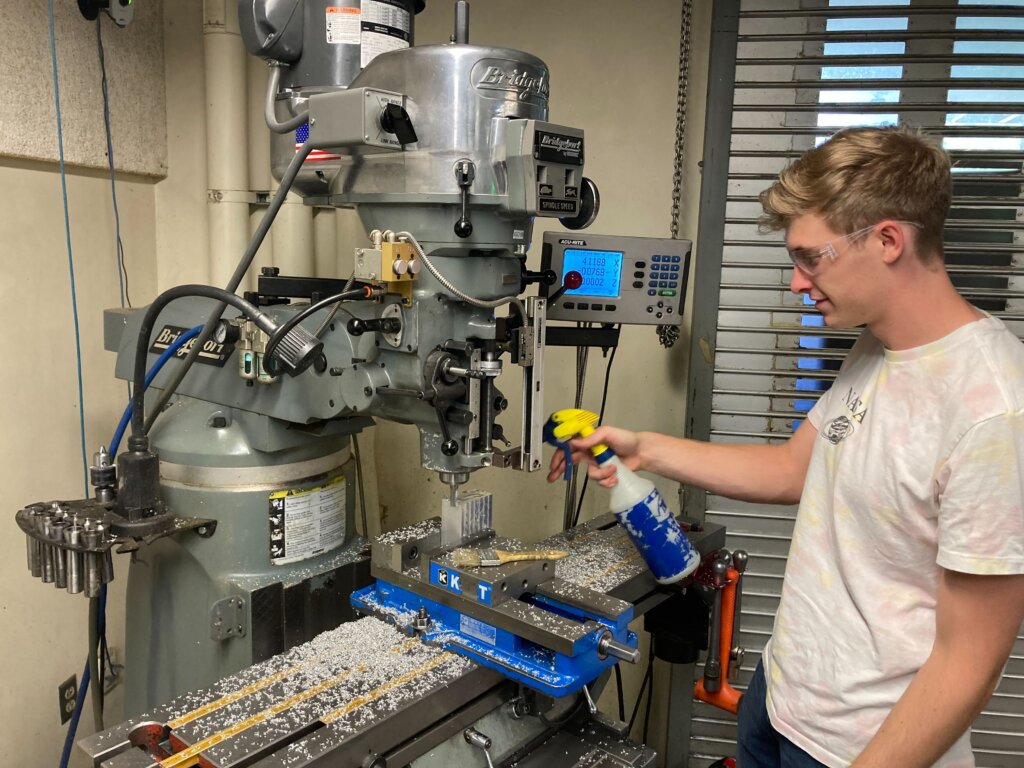
Nearing the Finish Line
The specialized teams that constitute LLEAP are coming together for the last lap of the project – a final design on track for next year.
“The project is becoming more collaborative as teams and students work together,” said Altamura, who has joined Miller to design a knee joint with more biomechanical accuracy for their senior project and LLEAP.
Two more senior projects focus on the linkages between the joints and soft goods, such as straps, for the suit.
Manufacturing has kicked into high gear this quarter, and teams are converging to implement controls and connect the prototype to software for the first time.
The software and simulation team had a recent breakthrough when members succeeded in getting the suit to dodge an obstacle during a simulation – a milestone moment, according to Max Lewter, chief operating officer and software lead for LLEAP.
Lewter, a fourth-year biomedical engineering major, joined LLEAP as a freshman and saw the project from pipeline to launch, then through COVID as members worked remotely to develop the first prototype.
Along the way, he found a passion for computer science and will graduate this spring with a minor in the discipline before moving on to pursue a master’s at Cal Poly.
“We did a ton of research and a lot of trial and error, but we’ve made incredible strides and now are seeing that work come to fruition,” he said. “This project has also helped me grow into a well-rounded engineer.”
Iourovitski and Gallagher launched LLEAP with the dream of helping a student walk again, while giving students like Lewter, Altamura and Miller a place to hone their skills and pass them down in a continuum of knowledge.
The impacts, though, have exceeded expectation.
“This project has brought more meaning and purpose than I’d imagined,” Iourovitski said. “People have landed internships, found friends, changed their majors and even the trajectories of their lives.”
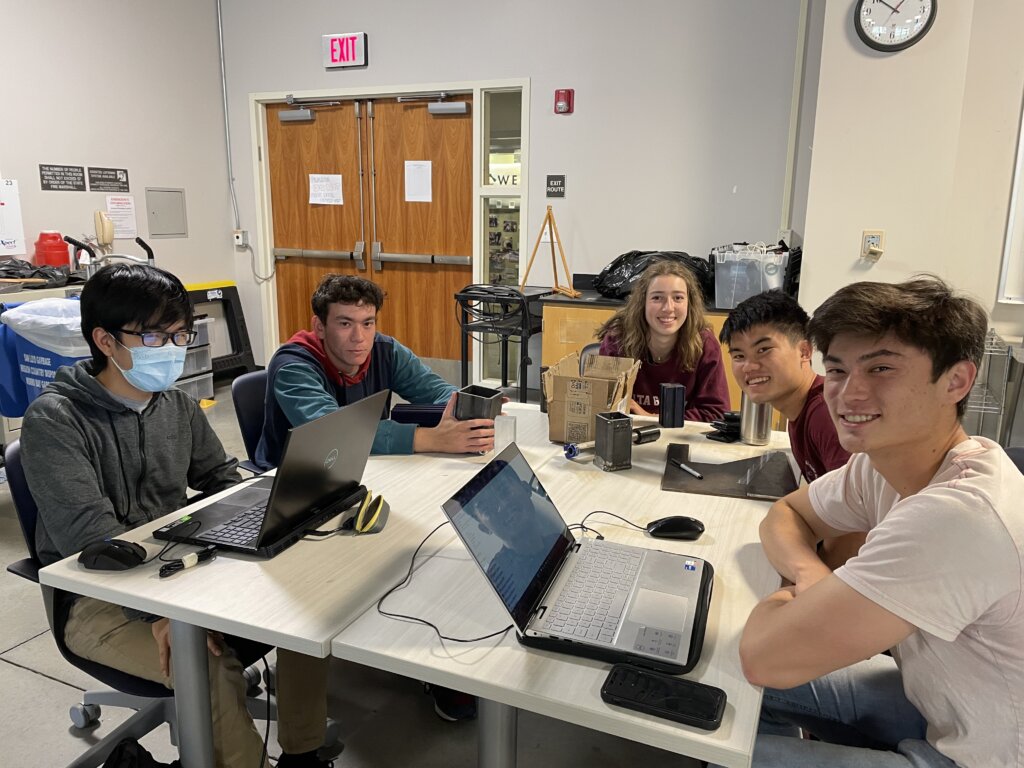
Donors step up
The Lower-Limb Exoskeleton Project started a crowdfunding campaign April 1 to raise $5,000 for development of its functional prototype.
In a generous show of support, donors Bruce Mengler (Computer Science, ‘76) and Sue Mengler (Computer Science, ‘75) contributed the entire amount. “When I saw the project, I quickly decided that I did not want LLEAP to fail due to lack of funding, and I could make sure it succeeded,” Bruce Mengler said.
Having met its first goal, LLEAP is now seeking $2,500 to manufacture the final cycloidal (hip design) and buy a battery for the exoskeleton. To donate, visit https://crowdfund.calpoly.edu/project/37218.
By Emily Slater