Melina Ruano was scared the first time she set foot in the Hangar machine shop.
The aerospace engineering freshman had to complete her red tag certification but had never seen a drill press, table saw or any such machinery while growing up in east Los Angeles.
“I don’t think I ever would have gone into the shop if I didn’t have to get my red tag,” she said. “I didn’t even know there were different types of screwdrivers!”
Ruano conquered her fear and completed her certification with the help of patient and friendly student shop techs who left a lasting impression.
“I remembered that experience and later thought that I would love to be that person for someone else, guiding them into the world of machining,” she said.
Now a senior, Ruano is proficient on the machines that once frightened her, shaping aluminum chess pieces with a lathe and cutting metal parts of a birdhouse with a water jet.
She is also building an inclusive, diverse shop culture as the lead student technician, hiring and overseeing the cohort of students who run Cal Poly’s machine shops.
“I want to make our shops even more welcoming because I believe those spaces are critical to the hands-on learning at Cal Poly,” Ruano said.
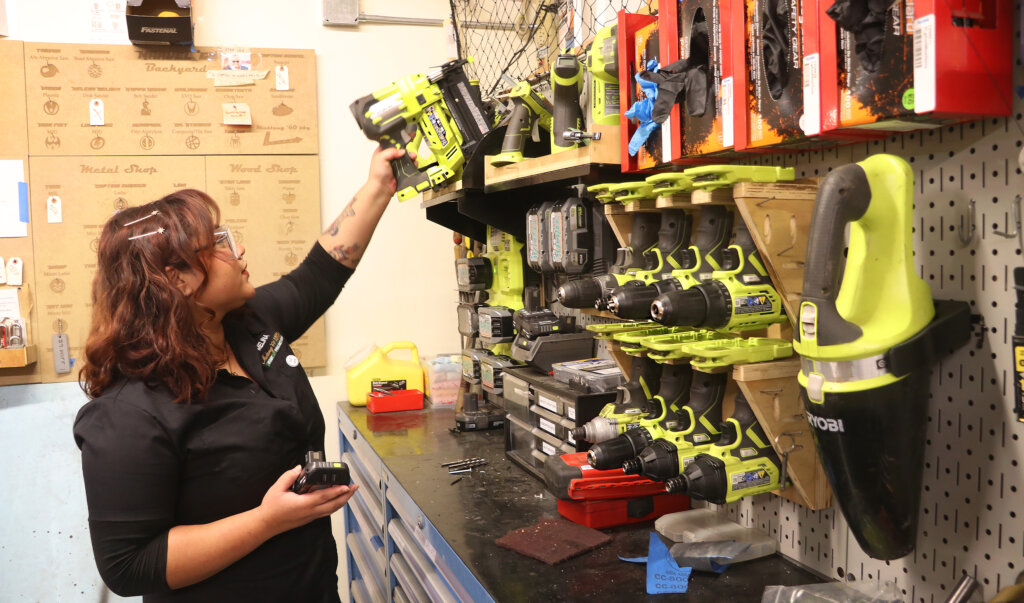
SOARING DEMAND
Cal Poly’s machine shops are employing 70 student shop techs – the most ever – this year to meet soaring demand, according to Eric Pulse, Mustang ‘60 machine shop manager.
Shop techs provide safety training for over 1,000 new users each year from any major on campus, a number that has grown with enrollment. Additionally, techs train almost all students in the College of Engineering in their first year.
Once students receive their red tag certification, they gain entry to shops in the Bonderson Projects Center and the Hangar facility to complete projects for classes and clubs and develop their technical skills.
A recent survey showed that shops are drawing students across almost 100 majors, plus staff members.
“When we returned to campus after COVID and our students realized the shops were still here, our usage peaked, and we haven’t come down from that level,” Pulse said.
He also pointed to expansion efforts over the last few years that have increased the capacity of the shops.
In 2019, improvements to an outside area at Mustang ‘60 bumped the square footage from 3,500 to 7,000, with the shop now averaging 45 users. And, on most Saturdays, the Hangar is hitting its 75-student capacity, which triggers a waitlist.
BY THE NUMBERS
Student-run machine shops are a rarity on college campuses, according to Pulse, who added that a program with 70 student techs is practically unheard of.
Cal Poly and Georgia Tech have the largest student-run shops in the country, he added, with Cal Poly certifying more students than any other university.
For every 10 students, one shop tech must be present to ensure tools and machines are used safely.
Shop techs are initially hired as “rookies” and receive training from junior and senior techs as they shadow them during their shifts. They can move up the ranks as they learn teamwork, leadership and communication skills.
“We want to hire shop techs who are approachable so that students feel comfortable enough to ask questions,” Ruano said.
Pulse echoed Ruano, adding that shop techs who readily engage with students have a greater chance of heading off poor decisions before they happen.
“In 20-plus years and at least half a million shop hours, the worst thing we’ve had happen is a few stitches on a finger,” said Pulse of the shops’ sterling safety record.
While about $180,000 of state and discretionary funds pay for equipment and facility improvements each year, the shop tech program is primarily funded by donors and industry partners.
BECAUSE OF THE SHOPS
Senior tech Aditya Garg, who is in his fifth year studying mechanical engineering, has played a critical role in the development of the expanded training program now in effect.
During fall quarter, students who had completed their red tag training could log 10 shop hours, plus an hour of cleanup to receive their yellow tag and access to mills, lathes and welders.
But Pulse said students were not getting enough coaching on the three machines, so he worked with Garg, the training supervisor, to ditch the yellow tag designation and revamp the program.
This quarter, students must log two shop hours and an hour of cleanup before taking any of the new intermediate-level training courses – two-hour training sessions for each of the three machines.
“The yellow tag training just wasn’t good enough,” Pulse said. “Now, students are getting dedicated skills training but with that comes a greater need for tech support.”
Pulse dreams of hosting weekend workshops where participants across the university could complete a fun project: “People could learn a new skill, try new tools and meet new people. The social aspect of the shops is undeniable.”
Garg has visions of advanced training on CNC machines, for example, that would remove the barrier to entry for clubs like Cal Poly Racing.
Fittingly, Garg chose Cal Poly after watching a racing club member make cuts with a CNC machine.
Garg had never seen such machinery before he and his mom wandered into Mustang ‘60 after losing their way on a campus visit. The club member directed Garg – a high school senior from San Jose – to the Hangar to see even more machinery and Garg was sold.
“I am at Cal Poly 100% because of the machine shops,” he said.
If you would like to support Learn by Doing experiences for student shop techs such as Garg and Ruano, please consider giving through this link.
By Emily Slater