Sophomore Kadin Feldis may be 3,300 miles from the Cal Poly campus, but he is putting the university’s Learn by Doing ethos to work in his hometown, creating hundreds of protective shields for local medical workers during the COVID-19 pandemic.
“To date, we have made about 200 face shields and have just partnered with two local companies to set up larger scale production,” said Feldis, a mechanical engineering major from Anchorage, Alaska. “A batch of about 200 more shields is underway at our new facility that is aimed at dramatically increasing production across the state.”
When Cal Poly announced that the remainder of the spring quarter would take place remotely, Feldis returned to his hometown, where, like many locales nationwide, medical workers didn’t have enough protective gear to protect themselves from the outbreak. After hearing about the need from friends and family on the front line, Feldis – then on spring break – decided to help.
His newly created business, FreeFloe Design, evaluated the needs and their own capabilities and decided to take on the face shield challenge. Feldis worked directly with Daniel Safranek, a physician and medical director of the Emergency Department at the Providence Alaska Medical Center.
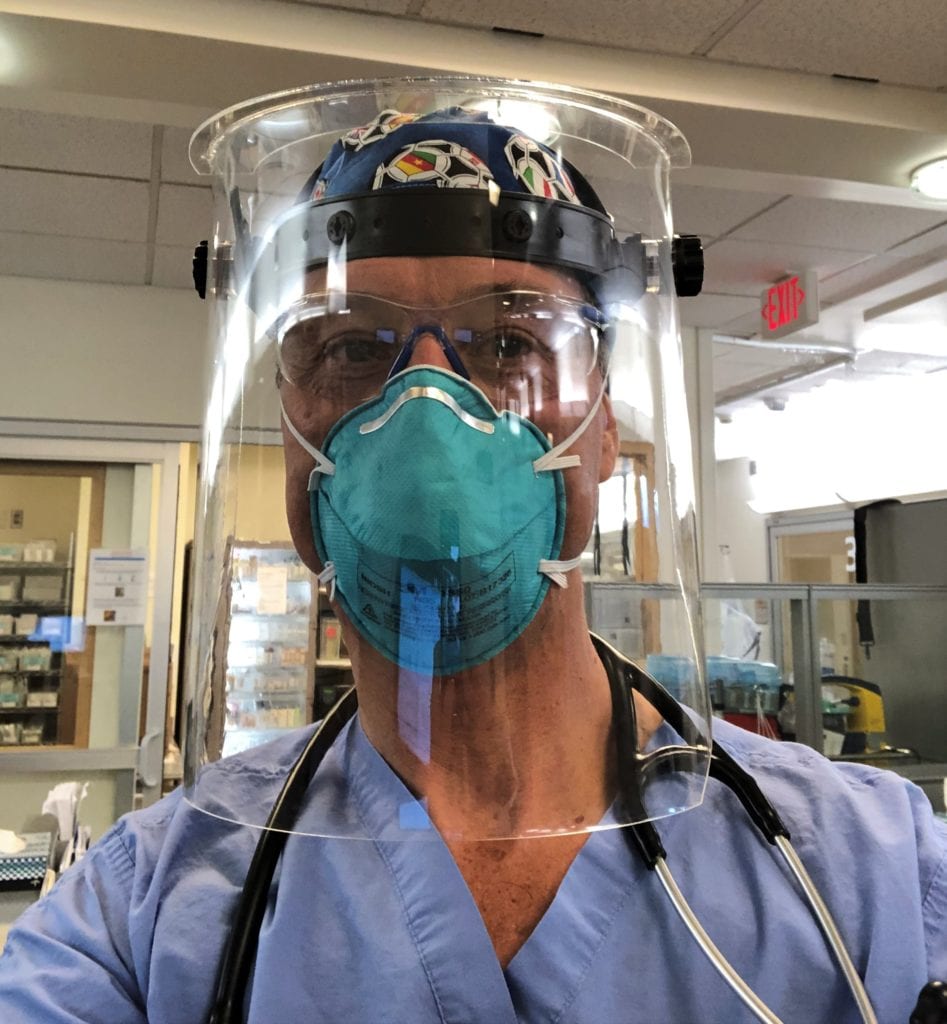
“He came up with the ideas and designs on his own and then had me look at them and provide suggestions,” Safranek said.
Feldis made the initial prototype in his kitchen.
“I used a knife to score the acrylic and snap out the shape for the lens,” he said. “The lens was then heated in the oven and formed over a plastic bucket.”
As the crisis spread rapidly, medical workers used almost every test version and iteration of the design. Those on the frontline gave feedback to Safranek, who then passed it on to Feldis.
“As we gather feedback, we make modifications to the design for out next production batch,” Feldis said.
Feldis designed every iteration himself and came up with the manufacturing process. Family members and volunteers helped with assembly and manufacturing.
“I cut the first 150 face shields on a laser cutter at the Anchorage Maker Space,” Feldis said.
Eventually, others stepped up. Companies like Dowland-Bach and The Launch Company donated laser and assembly/manufacturing time and offered forklifts and truck bays to organize the receipt of raw materials. Feldis has also received donations of industrial conveyor style ovens, and the Launch Company has offered a large portion of its local facility for manufacturing.
The shields he designed are more durable than others, he said.
“I think it’s really impressive that he’s taken the initiative to do this for his hometown. Seeing a need and developing solutions to help people is the definition of engineering design.”
Mechanical Engineering Professor Peter Schuster
“Most conventional face shields are made of thin, flimsy plastic and are meant to be discarded after a single use,” he said. “Our face shield, on the other hand, is made of thick acrylic mounted to the headgear from a welding helmet, creating a very durable and highly comfortable product that can be worn for 12-plus hour shifts.”
The hard plastic used is also easy to sanitize, unlike many other shields, and Feldis designed the shields to cover more of the user’s head than traditional ones, providing greater protection during procedures such as intubation.
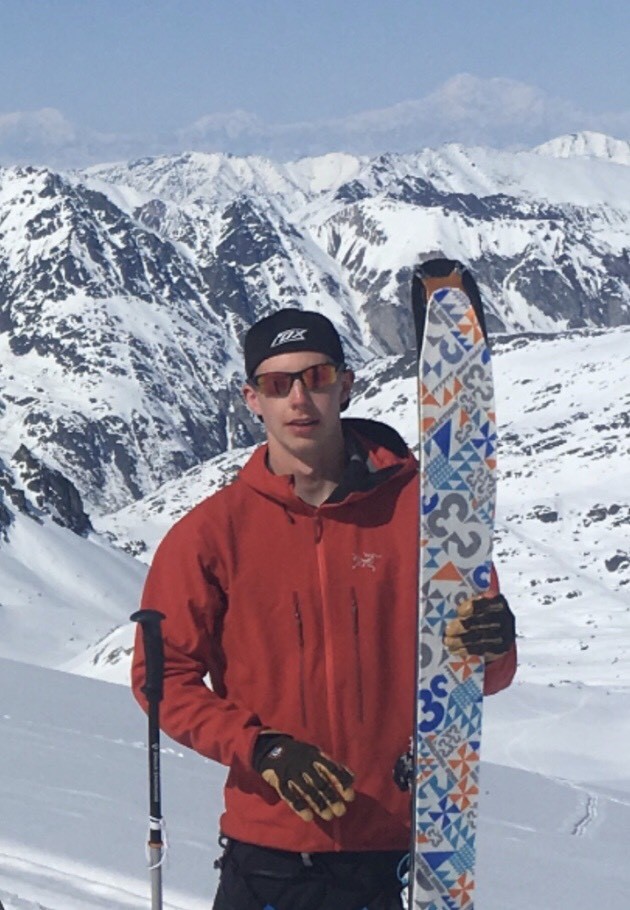
Safranek said the shields provided reassurance to staff members, who were taking strides to protect everyone from the virus.
“Kadin has done a fantastic job with this project,” he said. “He is organized and hardworking and seems comfortable reaching out to professionals with questions and ideas. He thinks big and follows up on his ideas.”
One of his professors, Peter Schuster, said Feldis shows how students contribute to Cal Poly’s success, using the skills and confidence the university has provided.
“I think it’s really impressive that he’s taken the initiative to do this for his hometown,” Schuster said. “Seeing a need and developing solutions to help people is the definition of engineering design.”
While having to leave campus has been a challenge for all students, Feldis, who is an avid volunteer and STEM ambassador in his hometown, said his work with the shields has been rewarding experience.
“The positive feedback has made my time spent on the project well worthwhile,” he said. “I am glad that I am in a position to help and am proud of the skills I have developed at Cal Poly and elsewhere that allowed me to take on this project.”
Feldis and his work on the shields was recently featured on KTUU, an NBC affiliate in Anchorage.